エジェクタピンとコアピンの豆知識
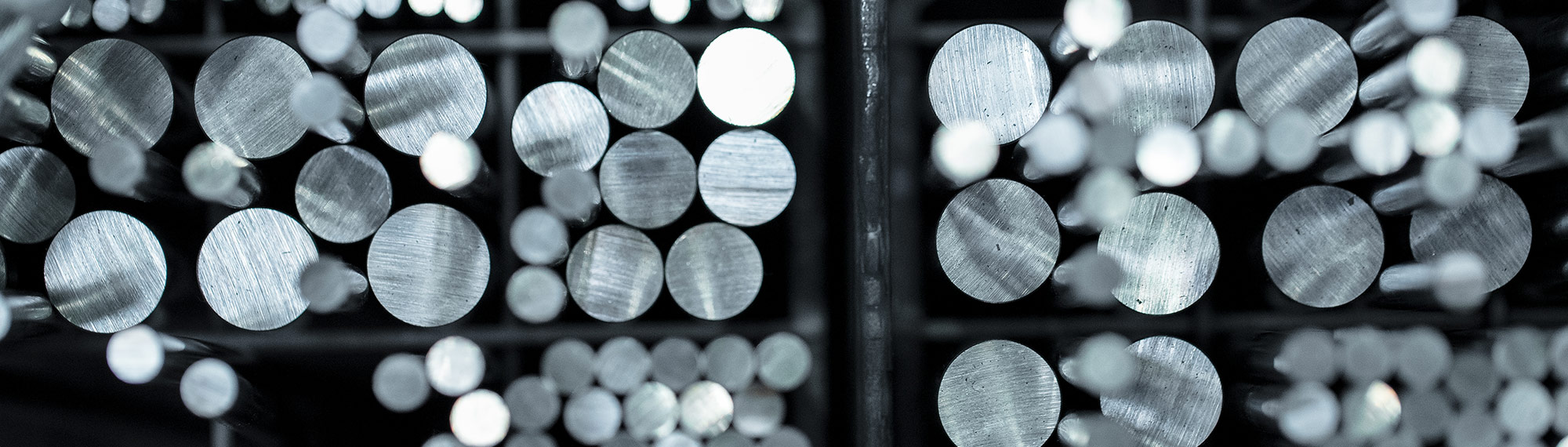
エジェクタピンの加工で用いられる摩擦溶接とは?
今回は摩擦溶接についてご紹介します。一部のエジェクタピン加工には、この摩擦溶接技術が採用されていますが、具体的にはどのような技術なのでしょうか?
摩擦溶接とは
摩擦溶接は、摩擦を利用して金属同士を接合する技術です。その歴史は古く、1957年に旧ソ連で実用化が試みられ、1958年には生産工程に導入されました。
摩擦溶接の原理
金属は規則的な結晶構造を持ち、自由電子と呼ばれる電子が結晶格子内を自由に動き回る性質があります。しかし、金属表面は酸化被膜や汚れ、吸着ガスなどで覆われており、この外部表面層がある限り、2つの金属表面は密着して接合することができません。
摩擦溶接では、回転運動と加圧による機械エネルギーを利用して、この表面層を除去します。この過程で発生する摩擦熱により接合界面の温度が上昇しますが、一般的にその温度は金属の融点を下回ります。高温・高圧下で金属表面が接触し、結晶粒の微細化が進むとともに、原子が拡散することで強固な接合が実現します。このプロセスはわずか数秒から数十秒で完了します。
摩擦溶接のメリット
- 高い再現性:同一条件での加工が可能で、安定した量産を実現します。
- 寸法精度の向上:通常の溶接に比べて変形が少なく、高精度に仕上がります。
- 異種材料の接合:接合条件を調整することで、異なる材質の接合も可能です。
エジェクタピンへの応用
当社では、エジェクタピンの頭部加工に摩擦溶接を一部採用しています。圧力、回転数、摩擦時間を厳密に制御し、専用治具を用いることで、鋼種や軸径、全長など多様な加工ニーズに対応しています。また、作業条件のプログラム化、品質記録の管理、PT(浸透探傷試験)や引張試験を通じて、確かな品質を担保しています。さらに、異種材料の接合技術を応用し、ハイブリッドコアピンの生産にも取り組んでいます。
今回は摩擦溶接技術のご紹介でした。当社の技術や製品についての詳細は、ぜひお問い合わせください。お客様のご期待にお応えできるよう努めてまいります。