エジェクタピンとコアピンの豆知識
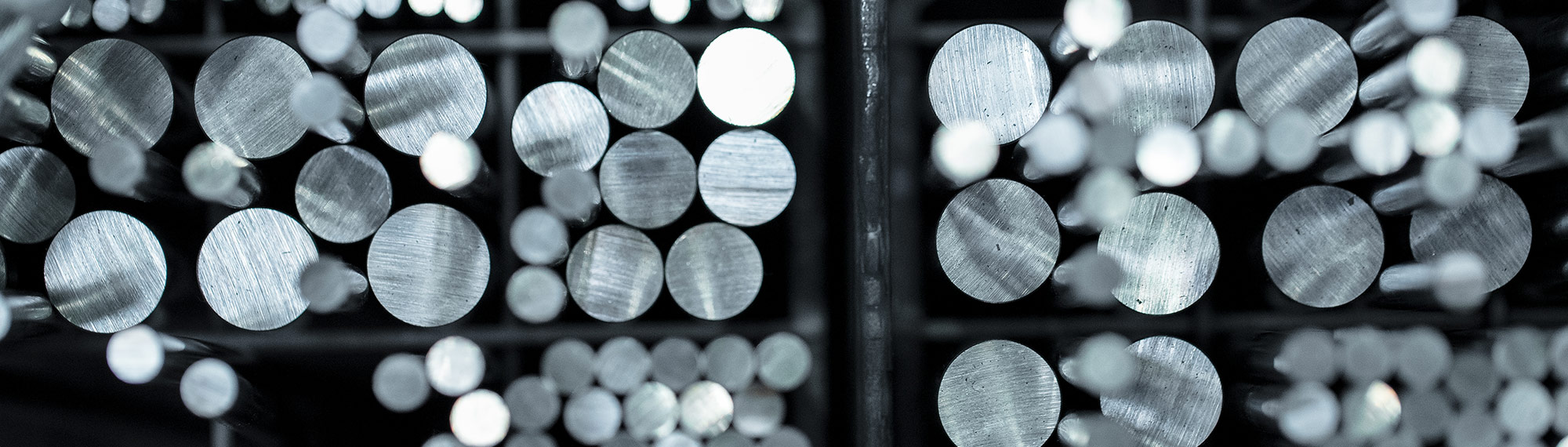
エジェクタピンの使用方法
今回はエジェクタピンの使用方法についてお伝えします。エジェクタピンは、金型成形において製品をスムーズに取り出すために欠かせない部品です。しかし、誤った使用方法により成形不良や金型の損傷を引き起こすこともあります。今回は、エジェクタピンの適切な使用方法について解説します。
【適切な使用方法】
1.材質の選定
エジェクタピンには様々な材質があり、成形品や使用環境に応じた選択が重要です。たとえば、高温環境では耐熱性に優れたDAC材が適しています。
2.配置の設定
エジェクタピンの断面積や本数を適正化することが重要です。まず、ダイカストの部分ごとに必要な離型力を計算し、エジェクタピンにかかる応力がどのピンにも均等にかかるように、ピンの径、本数、位置を決定します。
エジェクタピンの配置が不均等だと、押出し力に偏りが生じ、製品の変形や反りを引き起こしやすくなります。場合によっては製品の破損につながることもあります。特に薄肉成形品では注意が必要です。特定の離型力が一部のエジェクタピンに集中すると、座屈や折損の危険性も高まります。
配置のポイントは以下の通りです。
・エジェクタピンの数は、離型時にかかる応力が均等になるようにすること。
・座屈やダイカストの変形を避けるため、可能な限り大きな径のエジェクタピンを使用すること。
・薄肉部を押し出す際は、段付きエジェクタピンや半円形のエジェクタピンを設置すること。
・押出し力が一部に集中しないように、エジェクタピンをバランスよく配置すること。
・凸凹のピン跡が問題となる場合は、ランナーやオーバーフローの近くに設置すること。
・バリ取り作業の負荷を考慮し、後工程の機械加工面にピンを配置すること。
・後工程の追加工を考慮し、エジェクタピンの数量は必要最小限にとどめること。
3.長さの設定
エジェクタピンが短すぎると、成形品が金型から離れにくくなり、離型不良が発生することがあります。逆に長すぎると、成形品の変形やピン跡が目立つ原因となります。適切な長さのエジェクタピンを使用することが重要です。
4.クリアランスの確保
エジェクタピンと金型の穴のクリアランスが適切でない場合、ピンがスムーズに動かず、引っかかりや摩耗の原因になります。加工精度の高いピンを選ぶことも重要です。
5.使用中の管理
ダイカスト生産を継続すると、エジェクタピンには熱膨張や溶着が発生しやすく、摩耗や折損のリスクが高まります。例えばアルミ合金ダイカストの場合、一般的には数千から10万ショットを目安にエジェクタピンを交換しますが、交換時期は使用環境により大きく異なります。定期的に点検し、ショット数の記録を取り、摩耗や折損が発生する前にエジェクタピンを交換することが重要です。
まとめ
今回は、エジェクタピンの使用方法について解説しました。今後もエジェクタピンに関する情報をお届けしていきますので、ご期待ください!