エジェクタピンとコアピンの豆知識
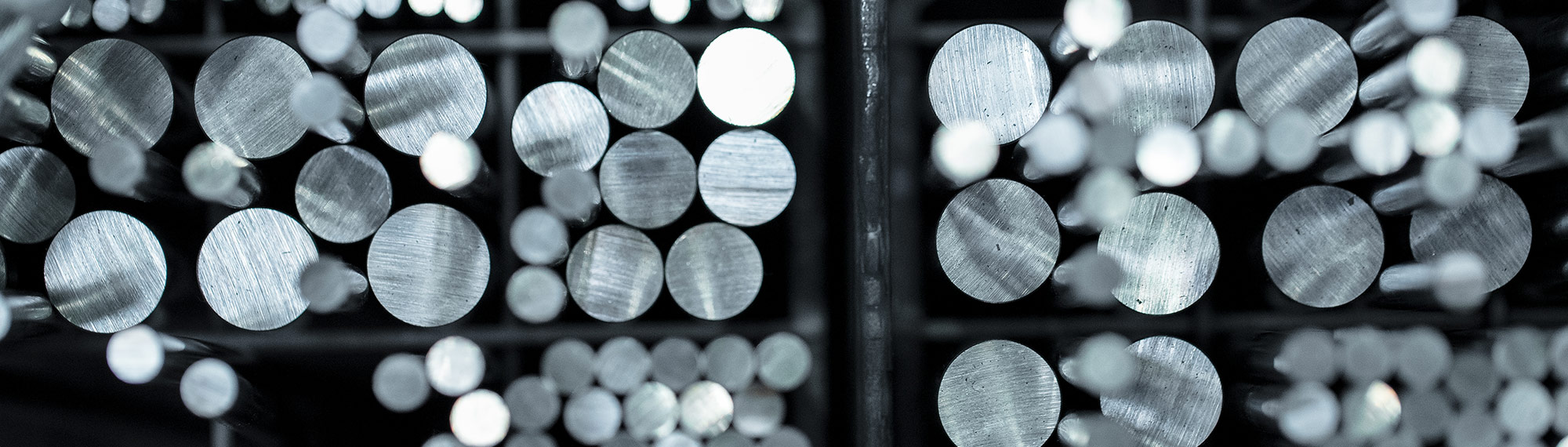
鋳バリの発生要因とエジェクタピンによる対策
当記事では、『鋳バリの発生要因とエジェクタピンによる対策』についてご紹介します。是非、最後までご覧頂き、ご参考ください。
鋳バリとは?
鋳バリ(鋳ばり)とは、鋳造欠陥の1種であり、金型の分割面の隙間、入子の隙間、エジェクタピンの隙間などに溶湯が侵入、凝固して発生した製品形状から張り出した突出部のことを指します。
鋳バリの発生要因
鋳バリの発生要因としては、大きく下記2点が挙げられます。
金型(エジェクタピン)
適切に鋳造不良を考慮した、設計がなされていない金型を使用することで鋳バリの発生につながります。例えば、金型に、0.05mm以上の隙間があると溶湯が侵入、凝固して鋳バリが発生します。また、エジェクタピン使用部分でも、エジェクタピンとピン穴とのクリアランスが大きいと、鋳バリが発生します。逆にクリアランスが小さいと、エジェクタピンの変形や熱膨張などによる摩擦抵抗が大きくなり、摩耗によって発生した隙間へ溶湯が侵入、また、エジェクタピンの破損にもつながります。そのため、金型内部の隙間には、細心の注意が必要となります。
ダイカストマシン
ダイカストマシンの型締結力が弱いと、鋳造圧に負けて、型開きが発生する恐れがあります。これにより鋳バリの発生につながります。そのため、鋳造圧と型締圧のバランスを考慮し、製品重量や大きさに応じたダイカストマシンの選定が重要となります。
鋳バリによる悪影響
では、この鋳バリが発生すると、どういった悪影響があるのでしょうか。主な悪影響は、下記の5点となります。
- 製品肉厚・質量増加や製品不具合
- 仕上げ工数の増加
- メンテナンス時間の増加
- ダイカストマシンの故障
- 製品を取り扱う作業者のケガ
上記のような悪影響を防ぎ、高品質なダイカスト鋳造品を製作するためには、鋳バリの発生を可能な限り抑えることが非常に重要となります。
そのためには、金型の設計やダイカストマシンの選定等に注意を配ることが最も大事です。加えて、ダイカスト鋳造に使用するエジェクタピンの選定も非常に重要となります。適切なエジェクタピンを選定することで、鋳バリの発生リスクを大きく下げることが可能です。
エジェクタピンによる対策
では、具体的にどういったエジェクタピンを選定し、鋳バリ発生の対策をすれば良いのでしょうか。鋳バリ発生を抑止するためには、下記の項目に注意し、エジェクタピンを選定しましょう。
①軸寸法・真円度
高精度な軸寸法と真円度に仕上がったエジェクタピンを使用することで、隙間を少なくし溶湯の侵入を防ぐことが可能となります。
②真直度
高度な真直度を持ったエジェクタピンを使用することで、ガタツキが抑えられます。これにより、上記と同様に隙間を少なくし、溶湯の侵入を防ぐことが可能となります。
③耐摩耗性
当然のことながら、エジェクタピンは、繰り返し使用されることで摺動部が摩耗します。そのため、耐摩耗性の高いエジェクタピンを使用し、摺動部の摩耗を防ぐことで、鋳造不良(鋳バリ)の発生を防止することができます。
④耐溶損性
耐溶損性の高いエジェクタピンを使用することにより、溶損によるエジェクタピンの減耗を防ぐことができます。これにより、溶湯が隙間へ侵入するリスクを低減することが可能です。
⑤高温強度
エジェクタピンは、高温環境で使用されるため、高温強度が弱いと、様々トラブルにつながります。そのため、高温強度が高いエジェクタピンを使用することにより、結果として、鋳バリの発生リスクの低下につながります。
上記の項目を満たしたエジェクタピンを使用することにより、鋳バリをはじめとした鋳造不良のリスク低減のみならず、ダイカストの生産性の向上を見込むことができます。
エジェクタピンのことなら秦精工にお任せください!
いかがでしたでしょうか。当記事では、『鋳バリの発生要因とエジェクタピンによる対策』についてご紹介しました。
秦精工では、高精度且つ、高耐久を兼ね備えたエジェクタピンの製作を得意としております。また、素材にSKD61よりも高靭性な株式会社プロテリアル製DAC®を採用することで、エジェクタピンによる鋳造トラブルの低減も併せて実現します。
さらに、当社では、エジェクタピンをΦ2からΦ20、最長1200Lまで幅広くラインナップしています。標準品は当社内で保管しており、最短で当日出荷にも対応します。また、お客様が重要視する項目に合わせ、形状、材質、熱処理、表面処理変更等のカスタマイズに対応することが可能です。
優れたエジェクタピンをお探しの皆様、お気軽に秦精工にご相談ください。